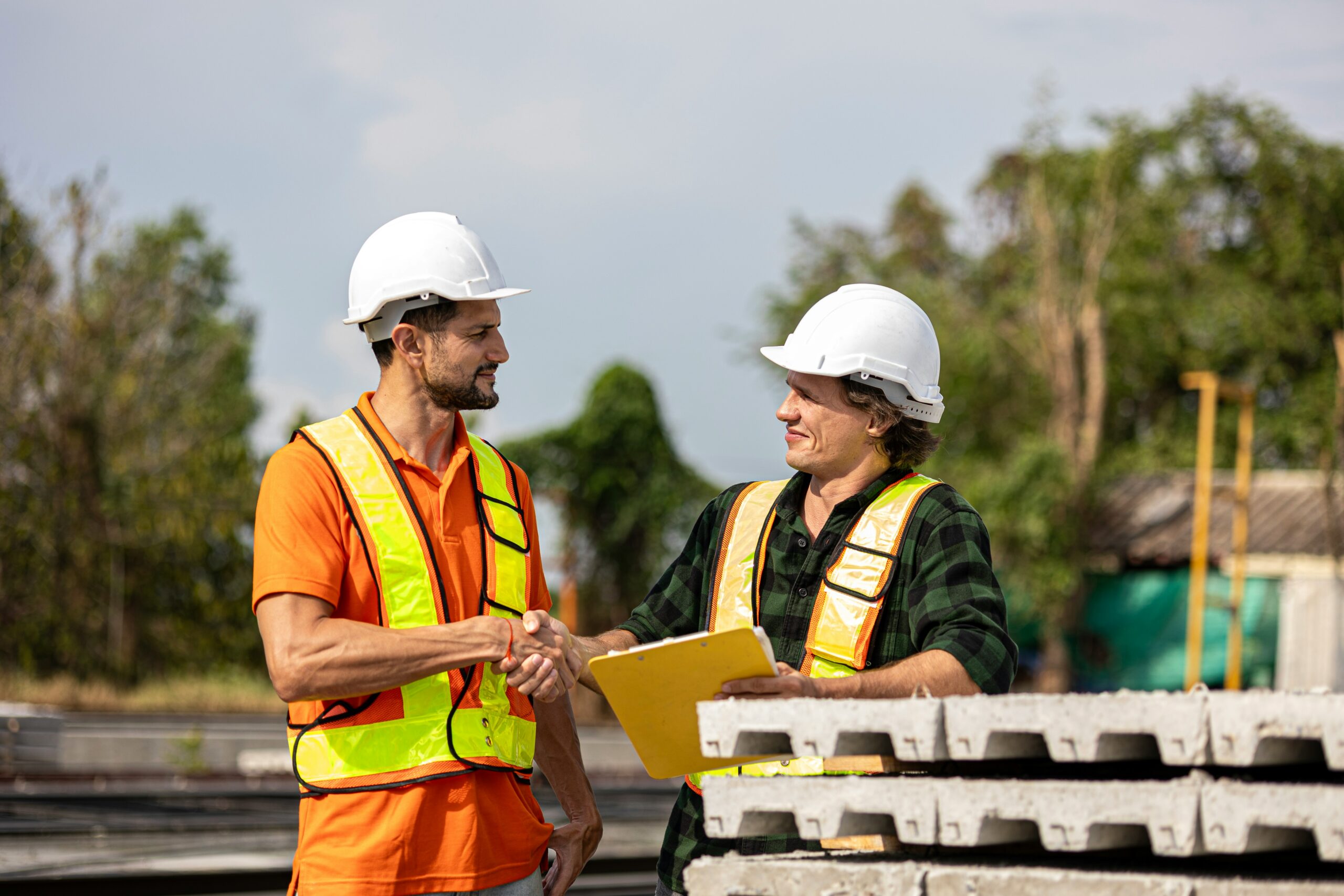
Managing subcontractors and suppliers effectively is key to the success of any project. When multiple parties work together, clear communication and coordination become essential. Projects face delays, cost overruns, and quality issues without proper management. This article explores how to coordinate subcontractors and suppliers to keep your project on track.
Understanding the Roles of Subcontractors and Suppliers
Subcontractors handle specific tasks within a project. They bring expertise in areas like electrical work, plumbing, or landscaping. Suppliers provide the materials and equipment needed to complete those tasks. Both play crucial roles, and their job depends on each other.
The relationship between subcontractors and suppliers must be smooth. If suppliers deliver materials late, subcontractors cannot do their jobs. Similarly, if subcontractors delay their work, suppliers may hold inventory unnecessarily. Understanding these dependencies helps avoid conflicts.
Clear Communication Builds Strong Partnerships
Clear communication is the foundation of managing multiple project partners. Establish open lines of communication from the start. Share project timelines, expectations, and deadlines clearly with everyone involved. Misunderstandings often arise from vague instructions or missed messages.
Use simple language to avoid confusion. Encourage subcontractors and suppliers to ask questions. Regular meetings and progress updates keep everyone aligned. You can share updates via phone calls, emails, or project management tools. The key is consistency.
Communication should flow both ways. Listen to subcontractors and suppliers about challenges they face. Sometimes delays occur due to unforeseen problems. Early warnings allow you to adjust plans without significant disruptions.
Set Clear Expectations and Agreements
Before work begins, clearly define each partner’s roles and responsibilities. Contracts or agreements should specify what is expected, including deadlines, quality standards, and payment terms. This clarity prevents disputes later.
Ensure subcontractors know what materials they require and when. Suppliers should confirm their delivery schedules. When everyone understands their part, the project runs more smoothly.
Setting expectations also includes safety and compliance standards. Make sure all partners follow the necessary regulations. This keeps the project safe and avoids costly penalties.
Plan and Schedule with Precision
Coordinating many moving parts requires careful planning. Develop a detailed schedule that includes subcontractor work phases and supplier deliveries. The schedule should be realistic and allow buffers for unexpected delays.
Avoid scheduling subcontractors before materials arrive. Confirm delivery dates with suppliers and communicate them to subcontractors. This prevents downtime and wasted labor costs.
Update the schedule regularly to reflect changes. If a supplier faces delays, adjust the subcontractor’s timeline accordingly. Flexibility is essential, but avoid frequent changes that confuse teams.
Use simple visual tools like calendars or Gantt charts. These help partners see the overall project timeline and their place in it. Visual aids improve understanding and coordination.
Monitor Progress and Quality Closely
Tracking work progress is essential to ensure the project stays on schedule. Visit the site regularly or require status reports from subcontractors and suppliers. Early detection of issues allows quick resolution.
Pay attention to quality. Materials from suppliers should meet specifications, and subcontractors must follow workmanship standards. Poor quality affects the entire project and can lead to costly rework.
When problems arise, address them immediately. Communicate concerns clearly and respectfully. Work collaboratively to find solutions rather than assigning blame. This approach maintains good working relationships.
Foster Collaboration and Mutual Respect
Projects succeed when all partners feel valued and respected. Encourage teamwork between subcontractors and suppliers. Cooperation improves when they understand the importance of their roles and how they impact each other.
Create opportunities for partners to meet and discuss the project. Building trust reduces conflicts and fosters a positive working environment. A collaborative atmosphere motivates teams to do their best.
Recognize good performance and timely deliveries. Positive feedback strengthens partnerships and encourages continued excellence.
Manage Payments and Documentation Efficiently
Timely payments motivate subcontractors and suppliers to perform well. Set up clear payment schedules based on completed milestones or deliveries. Avoid payment delays to maintain trust.
Keep accurate records of contracts, change orders, invoices, and delivery receipts. Organized documentation helps resolve disputes quickly and provides accountability.
Use simple digital tools to track payments and documents. This reduces errors and saves time compared to manual processes.
Address Risks and Prepare Contingencies
Every project faces risks such as supplier shortages, labor strikes, or weather delays. Identify potential risks early and plan how to respond.
Have backup suppliers or subcontractors ready if needed. Communicate contingency plans with all partners so they are prepared.
Being proactive helps reduce the impact of unexpected events. It also shows your leadership and commitment to the project.
Embrace Technology for Better Coordination
Technology can improve how you manage subcontractors and suppliers. Project management software lets you share schedules, documents, and updates in one place.
Mobile apps allow subcontractors to report progress from the field instantly, and suppliers can update delivery status in real time. This transparency keeps everyone informed.
Choose simple tools that your partners can easily use. Training may be necessary to ensure adoption. When used well, technology saves time and reduces errors.
Leading with Clear Focus and Teamwork
Managing subcontractors and suppliers well involves clear communication, careful planning, and building trust. When project partners work together smoothly, they reduce delays and improve quality.
Focus on open dialogue, set expectations clearly, and monitor progress regularly. Handle challenges quickly and fairly to keep momentum.
Strong coordination creates a positive work environment where everyone understands their role. This leads to successful projects and satisfied partners.
By following these principles, you can lead your team of subcontractors and suppliers to deliver projects on time, within budget, and to the expected standards. Effective management turns many moving parts into a well-oiled machine.